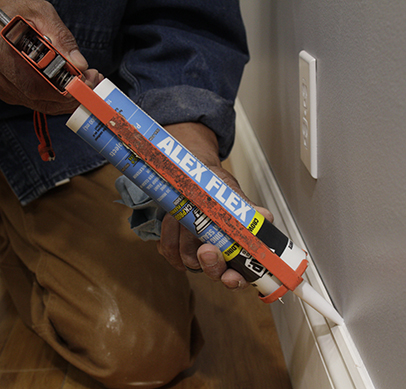
How to Install Baseboards
Follow this step-by-step for a room with decidedly more impact.
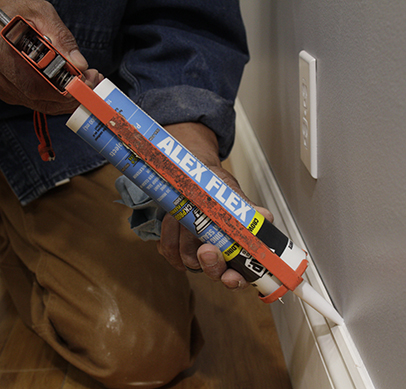
-
How to Install Baseboards and Chair Rail Step-by-Step
How to Install Baseboards and Chair Rail Step-by-Step
Tools
- Miter saw
- Tack cloth
- Paintbrushes
- Stud finder
- Pencil or painter's tape
- Level
- Brad nail gun
- Coping saw
- Tape measure
- 100-grit sandpaper
- 180-grit sandpaper
- Hammer
- Nail set
- Wood rasp
- Finishing tool
- Gloves (optional)
Painting walls is a fantastic way to freshen up a room. But don’t stop there. Go the extra mile by replacing worn baseboards or installing them for the first time with baseboard that has an attractive profile. With the right tools and products, a few key joint-making techniques, and our tips on how to cut baseboard, this is a fairly easy project that pays off big. Want to take it all to new heights? The same techniques apply to installing base shoe molding and chair rail too.
Remember: Wear proper safety gear, including eye and ear protection, when working with power tools.
Step 1: Rough-Cut Molding
Rough-cut molding at least 2 inches longer than needed. On pieces that will need to be spliced (see Step 8), allow an extra 6 inches.
Step 2: Sand, Prime and Paint Molding
If the molding you purchased is bare wood, sand with 100-grit sandpaper and wipe off dust with a tack cloth. Prime with Zinsser Bulls Eye 1-2-3 Primer. It covers stains and marks, seals and provides a smooth surface for paint. Mildew and mold resistant, it dries in one hour. When the primer is dry, lightly sand with 180-grit sandpaper. Wipe off with tack cloth and apply the first coat of paint.
Step 3: Locate and Mark Studs
Use a stud finder and mark stud locations with a pencil or, if you don’t want to put marks on the wall, a small piece of painter’s tape.
Step 4: Mark Molding Placement
For baseboard placement, use the floor as your guide. For chair rail, measure up from the floor and mark where you want the top of the molding. Then use a level to mark its location across the wall.
Step 5: Learn to Make Joints
Installing molding requires making several kinds of joints with miter and coping saws. We walk through this and show you how to cut baseboard corners in the most precise way possible.
Mitered Outside Corners
Before cutting the actual molding, make test joints with scrap pieces to find the exact angles. Miter the joints of outside corners (where molding meets molding) by cutting each piece at a 45-degree angle. If the corner isn’t square, the 45-degree miter cuts might not align perfectly. In that case, start at 46 degrees and adjust the angle until the test joint is tight.
Inside Corners
You have two joint styles to choose from:
- Mitered: Each piece of molding that meets at the corner is cut at a 45-degree angle on the corner ends. These are easier joints to make than coped joints but may be more visible as the molding naturally expands and contracts. You can, however, seal any gaps with caulk or sealant.
- Coped: For this joint style, cut the first piece of molding at 90 degrees and place it flush against one wall and into the corner. Cut the other piece at 45 degrees and then contour with a coping saw to make it fit tightly against the first piece. Coped joints are more difficult to make but work well when walls are out of square, meaning they don’t come together at right angles.
Molding at Door Trim
Either butt the molding to the trim or cut the end of the molding at a 45-degree angle about 1 inch back from the trim.
Molding at an Untrimmed Archway
You have several options:
- Cut the end of the molding at 45 degrees, about 1 inch back from the archway.
- Create a mitered joint at the corner of the archway and continue the molding around the corner.
- Create a molding return: Stop the molding an inch back. Cut the end at 45 degrees and then cut a short return at 45 degrees.
Step 6: Cut Molding for the Longest Wall
If you have a piece of molding that’s long enough to span the entire length of the longest wall and it’s between two inside corners, measure the length and cut the piece about 1/16 inch longer than needed. Square-cut the ends. If it’s going from an inside corner to an outside corner, cut the long piece of molding about ½ inch longer. Then use scraps of molding to test fit the outside corner: Make 45-degree miter cuts on the test scraps. If the corner isn’t quite square, start with 46-degree cuts and tweak as needed. Cut the end of the long piece of molding that will be at the outside corner to match the test cuts.
Step 7: Start at the Inside Corner
For inside corner to inside corner installation: Place one end of the molding into the corner, bow it slightly to fit and press it into place. However, don’t force the piece in. If it’s too tight, trim off a bit and try again. Nail the molding into the studs using a brad nail gun and 1½-inch brads. For inside corner to outside corner, test fit the molding, then nail into place.
Step 8: Splice When Needed
If you don’t have a piece of molding long enough to cover the entire wall, splice two pieces together with a scarf joint. Simply position the joint so that it lands over a stud. Then measure each piece, cutting about 1 inch longer than needed and at a 30-degree angle on the ends that will be spliced. Position and nail in place, including at the joint.
Step 9: Make a Coped Joint
Install molding on the other wall of the inside corner, creating a coped joint in the corner. Mark the direction of the cut with a slash mark. Set the molding upside down on the saw and cut at a 45-degree angle. Then clamp down the piece and use a coping saw to follow the line defined by the molding profile and the 45-degree cut you just made. As you cut, tip the saw at an angle, to create a back bevel. Fine-tune the cut with a rasp.
BONUS TIP:
If the coping saw blade tends to slide to one side as you start a cut, make a small starter notch with a utility knife. Make sure the teeth in your coping saw point toward the handle. That way, the blade will cut smoothly on the pull stroke. Also, don’t force the saw forward. Make even strokes, applying only light pressure and letting the blade advance at its own pace.
Step 10: Continue Around the Room
Work your way around your space, installing baseboard on the other walls.
Step 11: Miter Outside Corner
Test fit using scraps: Cut each piece at a 45-degree angle. If the corner isn’t square, make 46- degree cuts and fine-tune until it fits. When you’ve achieved a perfect corner, cut the molding and nail it into place.
Step 12: Use Adhesive Where Needed
To reduce the number of fasteners required to install baseboard or for hard-to-nail places, attach molding to the wall with DAP Dynagrip Heavy Duty Construction Adhesive. Apply adhesive bead in an “S” shape to the back side of the baseboard. You can also use a snozzle (a tool that spreads multiple rows of adhesive at once) by attaching the snozzle onto the nozzle of the cartridge. The Dynagrip formula’s powerful instant grab will hold the baseboard in place instantly and is repositionable for up to 10 minutes.
To attach very small pieces of molding (for example, if you opt for corner blocks on outside corners), use DAP RapidFuse Fast Curing All Purpose Adhesive. It sets in 30 seconds, cures in 30 minutes and cleans up with soap and water.
Step 13: Fill Brad Nail Holes
Brad nails should be below the surface of the baseboard. If any of them aren’t, you need to countersink them: Carefully hammer the brad nails until they’re nearly flush with the baseboard. Then place a nail set on the top of the brad nail and tap with a hammer to push the brad nail below the surface. Fill all brad nail holes with DAP Plastic Wood All Purpose Wood Filler. It is latex based and looks and acts like real wood but is low in odor and cleans easily with water. Don’t overspread the filler but do slightly overfill the holes. Let it dry, then sand it flush with 100-grit sandpaper.
Step 14: Seal Gaps and Cracks
Seal all gaps and cracks (where molding meets wall or other trim, or at joints) with DAP Alex Flex Premium Molding & Trim Sealant. Cut the tube’s nozzle at a 45-degree angle at the bead size required. Fill the gaps with sealant, then tool or smooth with a finishing tool. Let dry at least 30 minutes before painting.
Step 15: Finish Painting
Give the molding a final coat of paint.
-
Recommended Products
Product Recommendations
ALEX FLEX® Premium Molding & Trim Acrylic Latex Siliconized Sealant
High-performance sealant specifically formulated for use on molding and trim applications.
View ProductDAP RapidFuse Super Glue
RapidFuse Liquid Super Glue bonds in 30s, cures in 30min. Hybrid tech for durable, non-brittle bond. Clear, no mess. Indoor/outdoor, works on various materials.
View ProductDAP® Heavy Duty Construction Adhesive
DAP HEAVY DUTY construction adhesive is a premium high strength adhesive for heavy interior/exterior construction and remodeling projects.
View ProductPlastic Wood® All Purpose Wood Filler
A high quality, latex-based wood filler formulated to match various wood finishes—from a natural pine to dark walnut and several shades in between, including white.
View Product -
Related Projects
Related Projects
How to Paint Like the Pros
Follow these interior painting tips and tricks to give every room of your home that expert finish.
Read MoreSpackling 101
Learn to patch drywall and plaster like a pro with these spackling tips and tricks.
Read MoreHow to Patch Drywall
Follow this expert advice on how to fix a hole in drywall—no matter the size.
Read More